Digital Twins for construction – less risk and more return on investment
Digital Twins for construction – less risk and more return on investment for builders, architects and developers. While digital twins have been used for years in manufacturing and aviation, adoption is slowly making its way to construction.
A digital twin is a virtual model of a building that collects real-world information about the structure via sensors, drones and other wireless technology. The “twin” continuously learns from multiple sources, including advanced analytics, machine-learning algorithms and artificial intelligence (AI) to gain valuable insights about the performance, operation or profitability of a project, whether built or in progress.
Digital twins can be used to conduct tests, gain insight or record events and experiences without impacting the built object. A digital twin can also integrate historical data from past usage to compare deviation to a baseline.
What you should know
It’s important to note that a digital twin is a concept, not a single product or a piece of software, writes tech executive Vijay Raghunathan in Entrepreneur. In fact, the idea involves multiple technologies including 3D simulation, AI and cloud computing.
Twinning goes beyond a simulation to help users understand not only what can happen in the real world but what is happening in real time, he says.
This real-time reporting makes digital twins excellent for running simulations and trying out hypothetical scenarios before putting money or resources into a new construction project. The lessons learned from a twin can be applied to the original system with less risk and more return on investment.
Construction applications
A digital twin can be used for visualization, documentation, adherence to codes, modeling, analysis and planning. While twin tools are only being used sporadically in the construction industry, many industry watchers predict they will soon become an invaluable methods for pros like facilities managers, developers, architects, designers, builders, engineers and owners. Here are some common applications:
- A twin can help facilities managers know how a building is performing in real-time, which enables them to tweak performance to optimize efficiency. This data can be used for planning and designing future buildings, said Chitwan Saluja, digital technologies manager for Jacobs’ north division.
- Digital twins can prevent serious accidents by helping predict potential failures in systems like HVAC, water and electrical. This can save on time, resource costs and expensive shutdowns, said Saluja.
- They can help retail designers and developers create more profitable stores by providing data on the busiest times; where to place queues; and the correct indoor air temperature for optimal sales, said architect Zigmund Rubel, president and CEO of A Design + Consulting in San Francisco. “A digital twin can say that the temperature is too hot and this will affect sales in the retail section unless you change it by five degrees,” he said.
- Digital twins provide a project team with access to as-built and as-designed models, which are constantly synced in real-time. This allows companies to continuously monitor progress against the schedule laid out in a 4D BIM model, according to Intellectsoft.
- A twin can be handed over to the client to help support ongoing structural enhancements. The insight they provide can help inform future decision making and offer invaluable insight.
- In healthcare projects, digital twins help determine the number and placement of exam rooms, waiting areas and staffing needs. “Healthcare is taking off in terms of technology,” Rubel said. “Because the construction costs for these facilities are so high, there’s a lot more interest.” Staffing costs at medical centers are also high, so if digital twins can help save one nurse or doctor, they are really valuable.”
Roadblocks
While digital twin technology is expected to greatly benefit the construction industry in years to come, there are challenges to its adoption, said Saluja. First is the cost of the systems to create and manage digital twins.
“I would expect it will become a question of who will pay, which often comes back to the procurement method used for a project,” she said.
Because digital twinning requires a range of technology and software, creating a twin is not simple, Rubel cautions.
“There’s not one program that you just go in and buy shrink-wrapped off the shelf and then create a twin in a few days,” said Rubel. This means time and money must be spent to provide education and training to the team as well as investing in the necessary infrastructure. The cost varies greatly depending on the type of project, he added.
“Because it’s a new technology I think everyone has to realize that it’s going to be an investment,” he said.
While adding sensors into buildings and other built assets isn’t difficult, Saluja said, the hard part will be gathering the information created and exchanged during the lifecycle in a consistent and organized manner so that it can be reused without the need for extra investment of time and money.
Additionally, until twins are fully adopted, owners and contractors may not understand or appreciate how digital models can improve operation and maintenance. This means they are not asking for them or including them in design and construction budgets. If an owner does request a twin, sometimes its benefits are not fully implemented.
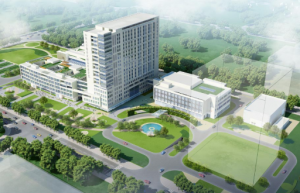
Notable projects
- Skanska USA created a digital twin using the indus.ai program for a student housing project at the University of California, San Francisco (UCSF).
- Chevron Corp. is using the technology to predict maintenance problems in its oil fields and refineries, according Supply Chain Management Now.
- Using its OneModel approach, Gafcon is applying digital twin technology to several projects, including the $1.2 billion JW Marriott expansion project in Los Angeles and the $1.5 billion redevelopment of San Diego’s waterfront.
- LiRo Group is testing the technology on the New York City Metropolitan Transit Authority’s $10 billion East Side Access project, for which it is construction manager.
- A Design + Consulting used digital models to help optimize the layout of a cancer hospital project in China, resulting in significant capital and operational cost savings.
Source: constructiondive.com