Roller Compacted Concrete- Properties, Advantages, and Applications
Roller-compacted concrete (RCC), which takes its name from the construction method used to build it, is a concrete of zero-slump consistency in its unhardened state. It is defined as concrete compacted by roller, as per ACI 207.5R.
This would ensure an effective consolidation which is crucial for achieving satisfactory density, strength (compressive strength can be more than 60MPa), smoothness, and surface texture. The roller compacted concrete is constructed without joints, formwork, finishing, steel reinforcement, or dowels.
These characteristics make roller-compacted concrete simple, fast, and economical. Roller compacted concrete owes much of its economy to high-volume, high-speed construction methods.
Nowadays, RCC is used when strength, durability, and economy are primary needs. It is applied for construction and rehabilitation of dams, roads, airfields, parking lots, power plants, road shoulders, storage facilities, military facilities, and other industrial complexes. Depending on the desired thickness and width of the installation, the concrete can be laid very quickly – from 60 up to 120 meters per hour.
Materials, Production, and Placement
Roller compacted concrete consist of the same basic ingredient as conventional concrete: cement, water, and aggregates, such as gravel or crushed stone. However, unlike traditional concrete, the mixture is drier and adequately stiff to be compacted by vibratory roller.
The mix design of RCC usually consist of a high amount of stone, Portland cement with a replacement of fly ash, a minimal amount of sand, and of course, water to hydrate the mix.
The mixture of roller compacted concrete need to be dry enough to avoid sinking of the vibratory roller equipment, but wet enough to allow sufficient distribution of the binder mortar in concrete during the mixing and vibratory compaction operations.
Roller compacted concrete is transported, placed, and compacted using earth and rockfill construction equipment.
Fig. 1: Roller Compacted Concrete
Characteristics of RCC
- Tough
- Durable
- Strong
- Sustainable
- Versatile
- Resist freezing and thawing

Advantages
The main advantage is reduced cost and time for construction (cost effective and Fast construction). so, it can achieve high quality in terms of strength, durability, and surface finish at relatively low device and personnel costs.
- Resistance to shoving and pushing
- Minimal maintenance required
- No rutting
- No pot holes
- Resistance to oil spills, fuels and/or hydraulic fluids
- Formwork costs are minimized or eliminated because of the layer placement method.
- Rebar is not required
- High Volume Placement
- It does not deform under heavy, concentrated loads
- Span soft localized subgrades
- Can withstand high temperatures
- Reduce cement consumption as the leaner concrete mix can be used.
- No concerns about high heat release while the concrete is drying.
- The cost of transporting, placement, and compaction of concrete are minimized because concrete can be hauled by dump trucks; spread by bulldozers and compacted by vibratory rollers.
Disadvantages
- Although it is used to efficiently design RCC dams to be the least cost alternate when compared to other types of dams, there are conditions that may make RCC more costly.
- Situations where RCC may not be appropriate is when aggregate material is not reasonably available, the foundation rock is of poor quality or not close to the surface, or where foundation conditions can lead to excessive differential settlement.
- Dams repaired or constructed with roller compacted concrete may suffer from water seepage. That is why water stoppage layers shall be considered.
Applications
Today, RCC is used when strength, speed of construction, durability, and economy are primary needs. It is a type of concrete pavement that is well suited for heavy industrial applications, as well as low-speed roads and arterial roads. The roller compacted concrete have been used to construct, repair, or maintenance of the following structures:
- Industrial and military facilities
- New dam construction
- Rehabilitation of existing dams
- Airports
- Storage
- Sub-base of roads and airfield pavements
- Ports
- Multi-modal yards
- Distribution centers
- Parking and storage facilities
- Streets & highways, intersections, shoulders, turn lanes, bike paths
- Manufacturing facilities, heavy haul roads, scrap yards
- Power plants and other industrial facilities
- Over-topping protection
- Reservoir liners
- Industrial slab floors
- Airfield maintenance areas
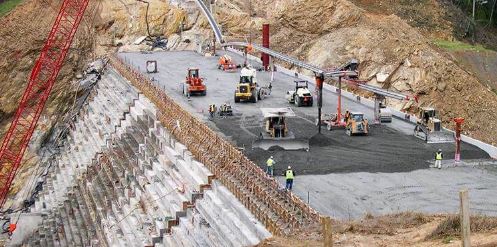
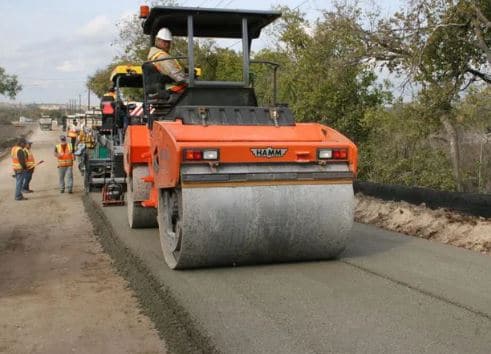
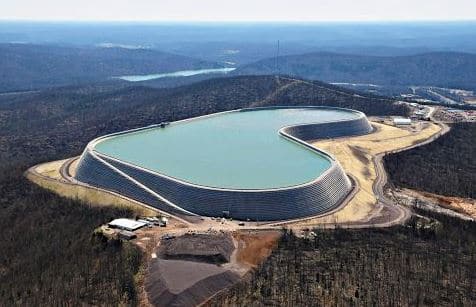